Como Realizar o Alinhamento de Motor a Laser com Eficiência
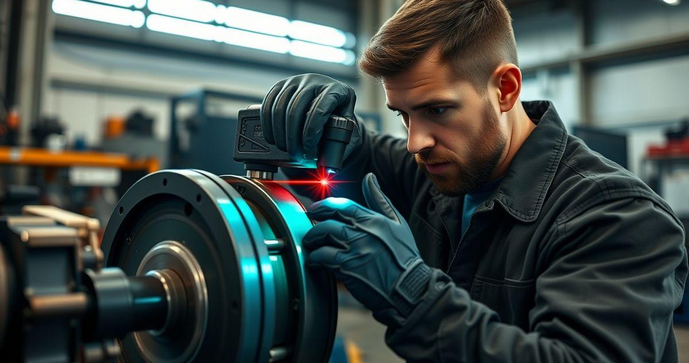
Por: Valdir - 23 de Maio de 2025
Conceito e Importância do Alinhamento de Motor
O alinhamento de motor é um processo fundamental que assegura que os eixos de um motor e seus componentes estejam corretamente alinhados em relação um ao outro. Um alinhamento adequado permite que os componentes do motor funcionem juntos de maneira harmoniosa, minimizando a vibração e o desgaste excessivo.
A importância do alinhamento preciso não pode ser subestimada. Quando um motor está desalinhado, pode causar uma série de problemas, como aumento do consumo de energia, falhas mecânicas e redução da vida útil dos componentes. Um motor desalinhado também pode afetar a eficiência operacional, resultando em custos mais elevados devido a manutenções frequentes.
Além disso, o alinhamento adequado é crucial para manter a segurança das operações. Um motor que não está corretamente alinhado pode provocar vibrações excessivas que, além de danificar o equipamento, podem representar riscos para os operadores e o ambiente de trabalho.
Em sistemas industriais, onde múltiplos motores e eixos interagem, o alinhamento correto é ainda mais vital. A falta de alinhamento em um único motor pode prejudicar toda a linha de produção, resultando em paradas não programadas e perda de produtividade.
Portanto, garantir que o alinhamento de motores seja realizado de forma precisa e regular deve ser uma prioridade nas práticas de manutenção industrial, contribuindo para a eficiência, segurança e sustentabilidade das operações.
Técnicas de Alinhamento de Motor a Laser
As técnicas de alinhamento de motor a laser são amplamente reconhecidas por sua precisão e eficácia. O uso de tecnologias a laser no alinhamento elimina erros comuns associados a métodos tradicionais, oferecendo resultados mais confiáveis.
Uma das técnicas mais comuns é o uso de alinhadores a laser, que consistem em um emissor e um receptor. O processo inicia-se com a instalação do emissor no eixo do motor, enquanto o receptor é posicionado no eixo da máquina acoplada. O sistema a laser irá projetar um feixe que permite medir o desalinhamento entre os eixos.
As etapas do processo incluem o seguinte: primeiro, instancia-se o alinhador a laser. Em seguida, é necessário fazer as medições iniciais para determinar o grau de desalinhamento. Após a medição, os dados são analisados para verificar se o motor deve ser ajustado para alinhar adequadamente.
Além disso, é importante realizar as correções necessárias com o método indicado pelo aparelho, que pode incluir ajustes de altura ou rotação. Uma vez realizados os ajustes, novas medições devem ser executadas para garantir que os eixos estejam perfeitamente alinhados.
Outra técnica inspirada no uso de laser é a metodologia de alinhamento em três pontos, onde medições são feitas em três diferentes posições ao longo do eixo. Isso proporciona uma análise abrangente, permitindo identificar desalinhamentos que possam não ser percebidos através de medições convencionais.
Por fim, a documentação das medições e ajustes é fundamental. Manter registros detalhados ajuda a monitorar o desempenho do motor ao longo do tempo e garante que os alinhamentos sejam feitos corretamente durante cada manutenção.
Equipamentos Necessários para Alinhamento a Laser
Para realizar o alinhamento de motor a laser de forma eficiente, é fundamental contar com os equipamentos adequados. O uso de instrumentos corretos não apenas aumenta a precisão, mas também facilita todo o processo de alinhamento.
O principal equipamento necessário é o alinhador a laser, que consiste em um conjunto de dispositivos que inclui um emissor de laser e um receptor. O emissor é fixado no eixo do motor, enquanto o receptor é posicionado no eixo do equipamento a ser alinhado. Esse sistema proporciona medições precisas do alinhamento entre os eixos.
Além do alinhador a laser, será necessário ter à disposição suportes para o alinhador, que garantem a fixação estável do aparelho durante o processo. Esses suportes permitem que o alinhador mantenha a posição correta, evitando desvios que poderiam comprometer as medições.
Outra ferramenta importante é a chave de fenda ou chave inglesa, que pode ser utilizada para ajustar as bases do motor ou da máquina, permitindo a correção do alinhamento conforme necessário. É essencial que essas ferramentas sejam de boa qualidade para evitar danificações nos componentes.
Um nível de bolha também pode ser útil para garantir que a base e o motor estejam corretamente nivelados antes de iniciar o alinhamento. Um motor perfeitamente nivelado contribui para a precisão do alinhamento feito com laser.
Por fim, recomenda-se o uso de um sistema de registro e documentação, que pode ser uma folha de cálculo ou um software especializado. Isso ajudará a manter um histórico de medições e ajustes realizados, permitindo um acompanhamento mais eficiente dos alinhamentos ao longo do tempo.
Benefícios do Alinhamento Preciso de Motores
O alinhamento preciso de motores oferece uma série de benefícios que impactam diretamente na eficiência operacional e na durabilidade dos equipamentos. Um alinhamento adequado contribui para um funcionamento suave, reduzindo a possibilidade de falhas e o desgaste prematuro dos componentes.
Um dos principais benefícios é a redução do consumo de energia. Motores desalinhados frequentemente geram maior resistência, levando a um aumento no consumo elétrico. Ao garantir que os eixos estejam corretamente alinhados, é possível otimizar o uso de energia e minimizar custos operacionais.
Além disso, o alinhamento preciso ajuda a prolongar a vida útil dos motores e de outros componentes mecânicos envolvidos. A ausência de vibrações excessivas e desbalanceamentos diminui o estresse sobre as partes móveis, promovendo um desgaste uniforme e evitando quebras inesperadas.
Outro benefício significativo é a melhoria nas condições de operação. Motores alinhados corretamente operam de forma mais silenciosa e estável, o que contribui para um ambiente de trabalho mais seguro e confortável para os operadores. Menos ruído também significa menos stress para as máquinas, reduzindo a possibilidade de manutenção frequente.
O alinhamento adequado também proporciona um aumento na produtividade. Um motor que opera de maneira eficiente é menos propenso a falhas, o que reduz o tempo de inatividade e melhora a continuidade da produção. Assim, as empresas podem atender a demandas sem interrupções.
Por fim, um bom alinhamento aumenta a segurança das operações. Motores que funcionam com precisão minimizam o risco de acidentes industriais e falhas catastróficas, protegendo não apenas o equipamento, mas também a saúde e a segurança dos trabalhadores.
Problemas Comuns em Motores Mal Alinhados
Motores mal alinhados podem causar uma série de problemas que afetam tanto o desempenho do equipamento quanto a segurança das operações. Reconhecer esses problemas é fundamental para realizar manutenções corretivas que garantam a eficiência do sistema.
Um dos problemas mais comuns é o aumento das vibrações. Quando os eixos não estão alinhados, a movimentação do motor gera vibrações excessivas que, além de causar desconforto, podem levar ao desgaste acelerado dos componentes mecânicos.
Outro problema severo decorrente do desalinhamento é o superaquecimento do motor. Quando um motor opera sob condições inadequadas, as partes móveis podem sofrer atrito excessivo, resultando em calor excessivo. O superaquecimento pode reduzir substancialmente a vida útil do motor e ocasionar falhas catastróficas.
Além disso, motores desalinhados costumam apresentar um consumo de energia mais elevado. A resistência gerada por um eixo desalinhado aumenta a carga sobre o motor, levando-o a trabalhar mais intensamente e, portanto, consumir mais energia elétrica.
Os componentes acoplados, como engrenagens e polias, também estão sujeitos a danos quando expostos à operação de motores desalinhados. O desgaste irregular pode levar à falha de peças que normalmente funcionariam de maneira eficiente.
Por último, um ambiente operacional mais perigoso é outra consequência significativa de motores mal alinhados. O aumento das vibrações e do ruído pode resultar em distrações para os operadores e até em acidentes, caso não sejam tomados cuidados adequados. Portanto, é vital manter os motores devidamente alinhados para promover um ambiente de trabalho seguro e eficiente.
Manutenção e Ajustes Após o Alinhamento
Após a realização do alinhamento de motores a laser, é fundamental implementar um plano de manutenção e ajustes regulares para garantir que a eficiência do alinhamento seja mantida ao longo do tempo. A manutenção preventiva ajuda a identificar e corrigir problemas antes que eles se tornem sérios.
Primeiramente, recomenda-se realizar verificações periódicas do alinhamento. Mesmo que um motor tenha sido recentemente alinhado, fatores como vibrações geradas por outras máquinas, cargas variáveis e desgaste de componentes podem causar desalinhamento ao longo do tempo. Realizar medições periódicas ajuda a garantir que o alinhamento permaneça dentro das especificações ideais.
Outra prática importante é a lubrificação regular de componentes móveis. A falta de lubrificação pode aumentar o atrito e a tensão sobre os eixos, contribuindo para o desalinhamento. Certifique-se de seguir as recomendações do fabricante quanto ao tipo e à frequência de lubrificação.
Além disso, deve-se observar os suportes e fixações do motor. Com o tempo, os parafusos podem se afrouxar devido às vibrações, o que pode afetar a estabilidade do motor e, consequentemente, o alinhamento. Inspecionar e apertar quaisquer conexões soltas é uma prática que deve ser incluída no cronograma de manutenção.
É aconselhável documentar todas as medições e ajustes realizados. Manter um histórico detalhado facilita o acompanhamento do desempenho do motor e ajuda a identificar padrões que possam indicar a necessidade de intervenções mais significativas.
Por fim, a formação e a capacitação dos operadores são essenciais. Ensinar a equipe a realizar inspeções básicas e a identificar sinais de desalinhamento ou desgaste pode prevenir problemas antes que se tornem críticos, promovendo uma operação mais segura e eficiente.
O alinhamento de motor a laser é uma prática essencial que não apenas melhora a eficiência operacional, mas também prolonga a vida útil dos equipamentos. Ao reconhecer a importância do alinhamento preciso, as empresas podem evitar problemas comuns, como vibrações excessivas e superaquecimento, que podem impactar negativamente a produção.
Investir em técnicas de alinhamento a laser, junto com um plano de manutenção regular, garante um funcionamento suave e eficaz dos motores. Além disso, a capacitação dos operadores é um aspecto vital para a manutenção da segurança e eficiência no ambiente de trabalho.
Em resumo, o alinhamento de motores deve ser considerado uma prioridade nas práticas de manutenção, contribuindo não apenas para a economia de energia e a durabilidade dos componentes, mas também para um ambiente de trabalho mais seguro e produtivo.